Products Used | SQC2S™ Cleaner STS™ |
---|---|
Product Types Used | Secondary Belt Cleaners |
Industry | Metals |
Customer | A plant in Para, Brazil |
Problem
A producer of aluminum oxide was experiencing excessive spillage and downtime on the main conveyor transporting 185 mt/h (203 st/h) of granulated bauxite. Inadequate performance from the primary cleaner caused material to cling to the return side of the belt, pile up beneath the conveyor, spill along the belt path into walkways and foul rolling components. To clean the belt, workers were constantly required to hose it down with water. When the existing cleaner wore out, 4 workers would take 3+ hours to change blades, requiring total disassembly of the equipment. Labor costs for cleanup, equipment, downtime and lost product were increasing the cost of operation.
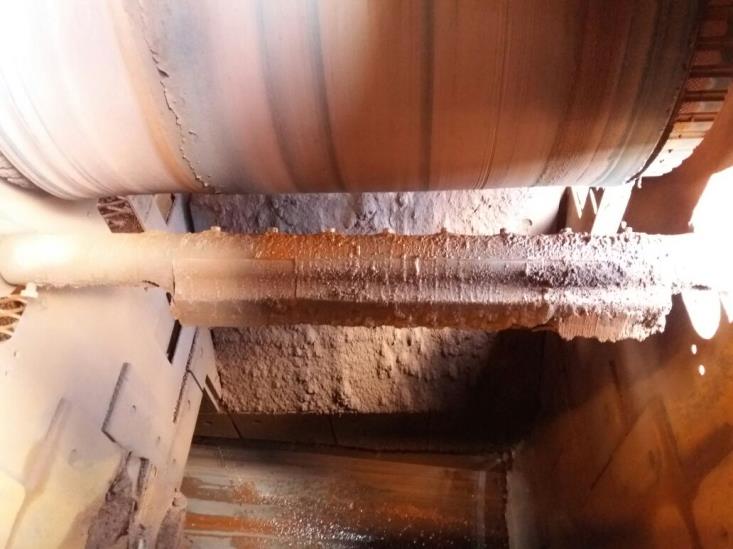
Solution
Having worked with Martin Engineering in the past, operators invited technicians in to examine the situation and offer a solution. After performing a Walk the Belt™ assessment, the crew installed a Martin® SQC2S™ Cleaner STS™. Located behind the primary cleaner, the unit cleans dust and fines adhered to the belt and trapped in cracks, introducing it back into the discharge flow. With individual tungsten-tipped polyurethane blade cartridges, the heavy-duty cleaner handles the most punishing applications. Mounted on a sliding mandrel, replacing the blade cartridges is an easy one-person procedure that takes only minutes to perform, with no reach-in hazard or extra labor required.
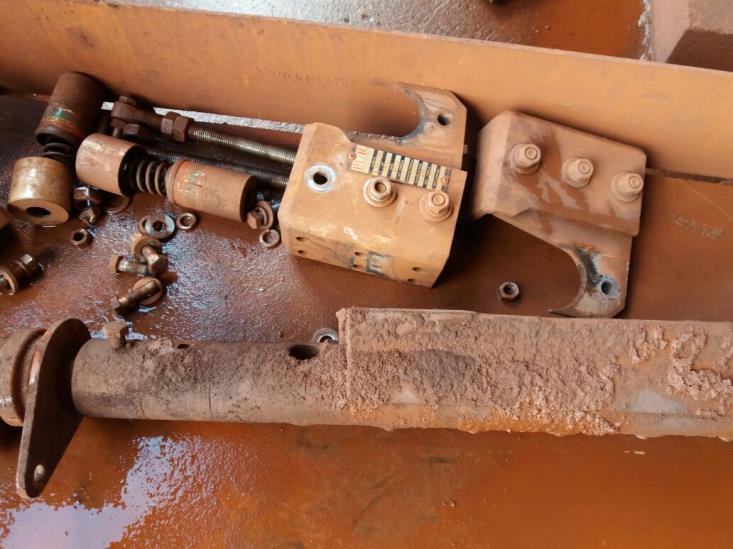
Result
After installation, operators noticed a drastic and immediate reduction in the amount of cargo clinging to and falling from the belt. Material no longer spilled onto walkways or fouled moving components. Cleanup and maintenance were reduced to a predictable routine of scheduled downtime. This improved working conditions and reduced the amount and cost of labor. "Everyone is very satisfied with the result," said the manager overseeing the project. "We're most impressed with the cleaning efficiency, resulting in fewer shutdowns." Operators continue to work with Martin Engineering on other bulk handling solutions.
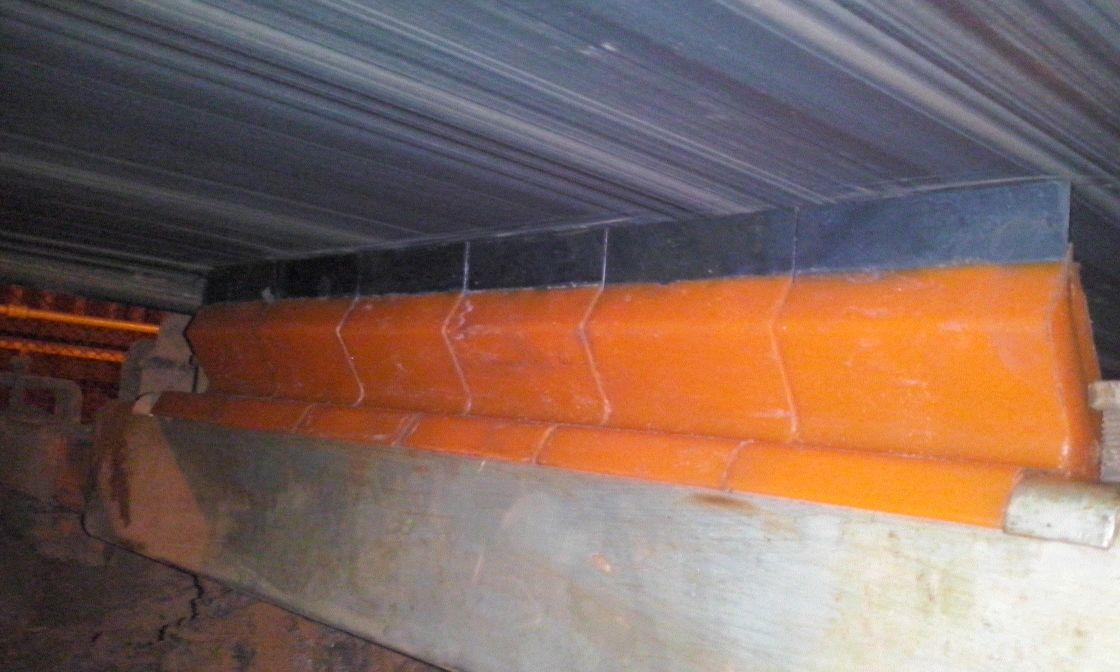