Products Used | ApronSeal™ Single Skirting |
---|---|
Product Types Used | Transfer Point Solutions , Belt Sealing |
Solutions | Installation |
Industry | Coal-Fired Power |
Customer | Platte Generating Station, Grand Island, NE |
Problem
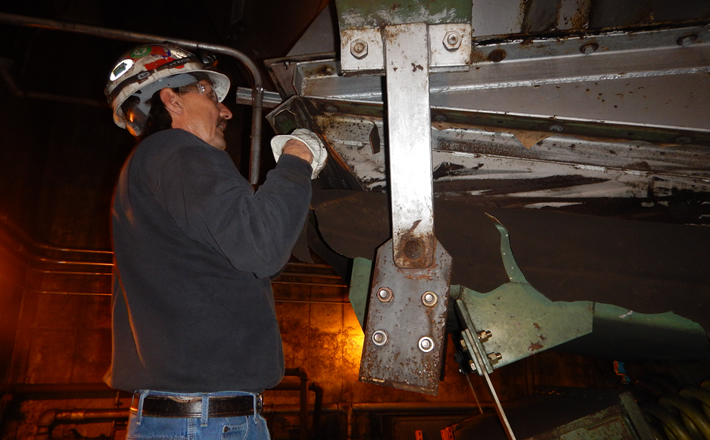
Platte Generating Station (PGS), a coal-fired power plant located in Nebraska handling a volume of approximately 30,000 tons per month of PRB coal, was experiencing failures of the rubber/fabric seals at the top of the chute wall on its Train Unload Vibratory Feeder. Unable to handle the powerful vibration, the thin rubber seals allowed dust and fines to spill from the chute. Workers had to clean up at least once per month, and the spillage created a potential workplace hazard.
Solution
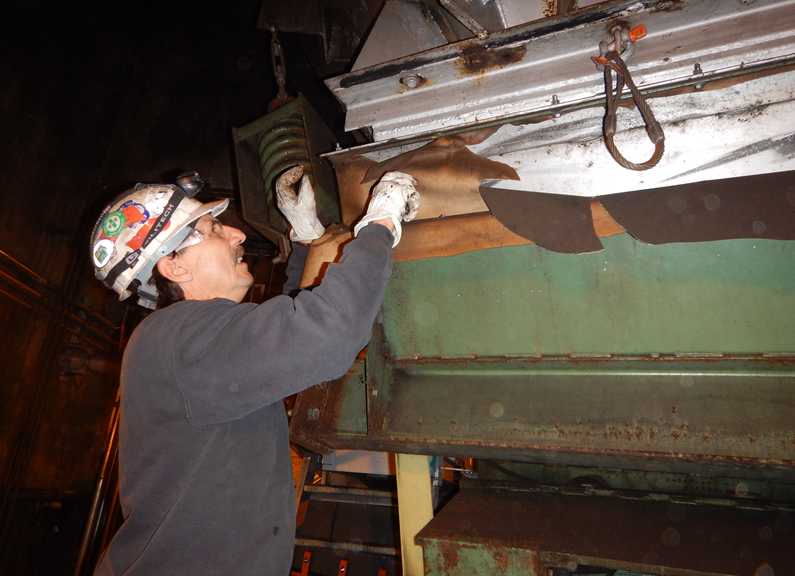
Martin technicians inspected the issue and came up with an innovative solution. After removing the original seal, a highly experienced technician performed a custom installation of a Martin® ApronSeal™ Skirting on the chute wall. Designed originally for sealing the bottom of high volume conveyor chutes, the EPDM rubber composite skirt offers excellent rigidity and stands up well to constant vibration. Utilizing a specially engineered single strip unistrut system that holds the rubber composite strips firmly into place, the assembly facilitates replacement of the seal safely from outside the chute.
Results
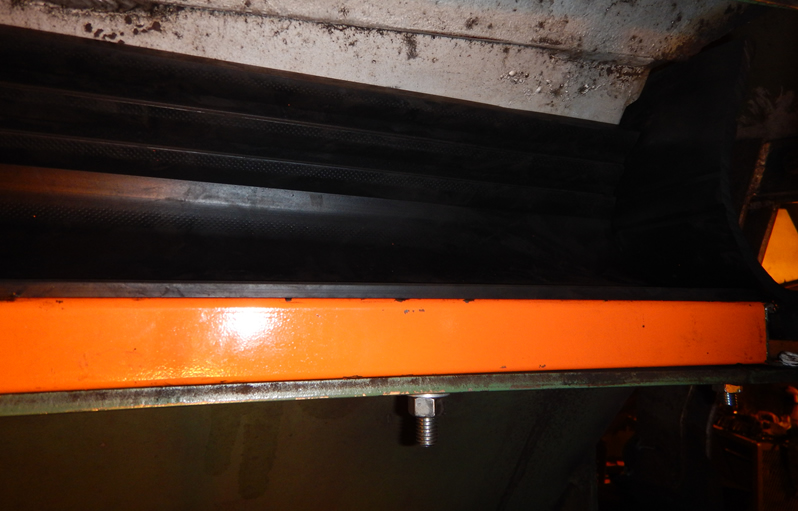
After a months-long trial period running several tons of coal, the Martin® ApronSeal™ Skirting has yet to require replacement. There has been a considerable reduction in spillage and maintenance labor. "The new Martin® ApronSeal™ Skirting holds up to the rigors of the vibratory feeder significantly better than any other type of seal we have tried," commented Ryan Schmitz, Production Engineer at PGS. Due to the rigidity and longevity of the ApronSeal experienced to date, and the associated reduction in airborne dust, plant managers have initiated the proposal process for another three units to be installed in other areas of the facility.
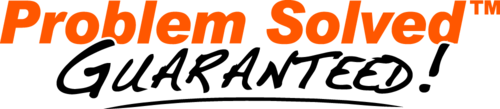
We've solved your problem somewhere before!
While your problem seems unique and frustrating, with 70+ years of solving similar problems around the world, and with the most experienced and educated people on our teams, we can assure you that we’ve “Been There, Done That.” At least close enough to know what needs to be done next and adjust for your situation.
Put Us To The Test For Free! Let Us Give You a Solution.