Load Your Cargo Correctly
Published: February 16th 2015
Before a conveyor belt is loaded, it has to be transformed into a shape that will carry bulk material. In this post and a few following, we will discuss the following points:
- Transition areas, the terminal pulleys and the first fully troughed idlers.
- Stabilizing the belt path before loading.
- Centering the belt on the structure.
- Troughing the belt into desired profile.
- Sealing the back and edges of a load zone to prevent spillage.
Centering The Belt
Having the belt in the center of the conveyor structure as it goes in to the loading zone is very critical. If the belt is not properly centered when it receives the load, the force of the load will increase belt misalignment. The area between the pulley and load zone is very small and the belt has too much tension to allow mistracking correction here, so belt-centering devices are installed on the conveyors return side to make sure that the belt is centered as it enters and exits the tail pulley. If the belt is centered at the entry of tail pulley and mistracks between the pulley and load zone, the most likely problem is that the pulley is out of alignment. Having a straight tail pulley and tracking device assures the belt enters centered in the load zone.
Tail Pulleys - Wings and Wraps
Winged type tail pulleys are often installed as a method to reduce the risk of belt damage from the entrapment of lumps of material between the belt and pulley. These pulleys have vanes that resemble a paddle wheel on a steamboat. This design allows material that would have been trapped between a solid pulley and the belt to pass through the pulley face. Between the pulleys crossbars are inclined, valley-shaped recesses that prevent fine or granular material from being caught between the tail pulley and return belt. These valleys provide a self-cleaning function - there is very little surface area where material can accumulate and the rotation of the pulley throws the material off the pulleys face.
Despite the design, wing type tail pulleys are still subjected to buildups and material entrapment and often do not provide the desired protection. They are successful on slow moving belts. The most significant drawback of wing pulleys is the oscillating action they introduce to the belt path. The wings of the pulley introduce a pulsating motion that destabilizes the belt path and adversely affect the sealing systems. CEMA recommends that wing pulleys not to be used for belts travelling over 2.25m/sec.
Spiral Wrapped Wing Pulleys
A better choice than the conventional winged pulley is a spiral wrapped tail pulley. These pulleys have an additional steel strip wrapped in a spiral around the pulley circumference. The steel band is wrapped over the top of wings in two spirals, converging in the center from each end of the pulley. Wrapping the band of steel around a wing pulley allows the pulley to provide self-cleaning but eliminates the oscillation action imparted to the belt. Existing wing pulleys can be upgraded with narrow 2 to 3 inch steel strips welded around the outside edge of the wings.
Crown Pulleys
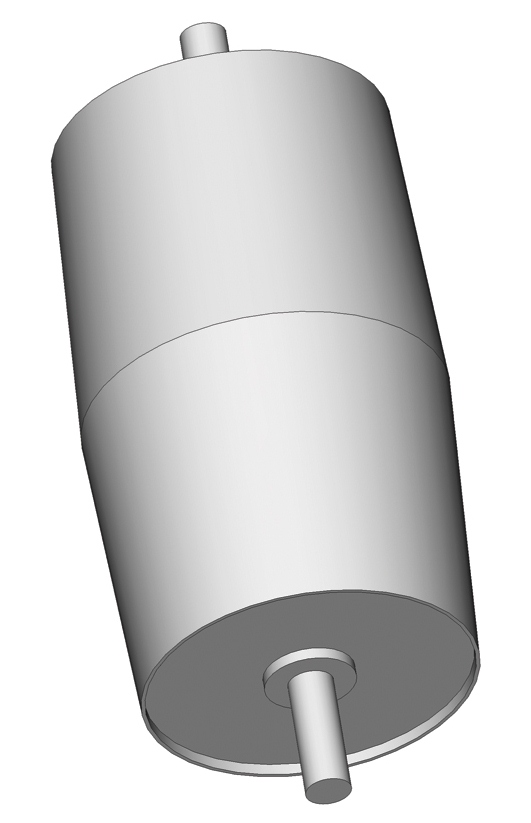
A crown faced pulley changes in diameter from the outer edges to the center of the pulley, with the center being slightly larger than the edges. Crown faced pulleys are sometimes used at tail ends assuming that it will improve the tracking of a belt as it goes around the pulley into a loading zone. However crown faced pulleys can also damage the belt if used in high-tension areas. In these high-tension areas, additional diameter in the center of the pulley adds additional stress to the center of the belt and may cause carcass and lagging damage.
The best solution to prevent material build up on a tail pulley is to use a solid flat steel pulley, protected by a cleaning device located directly in front of pulley. This diagonal plow or VPlow should be mounted directly in front of the tail pulley on the non-carrying side to remove the fugitive material.
Pulley Lagging
Conveyor pulleys should be covered with some form of fabric, ceramic or urethane. Lagging is used on a driving pulley to increase the coefficient of friction between the belt and pulley. Lagging also reduces abrasive wear on pulley face and to effect a self-cleaning action on the surface of pulley. Abrasive wear and material buildup can substantially reduce pulley life. Drive pulleys should always be lagged. Non-driving pulleys especially on the carrying side of the belt should be lagged whenever abrasive or build up conditions exist.