Efficient Handling of Coal on Belt Conveyors
Published: June 7th 2013
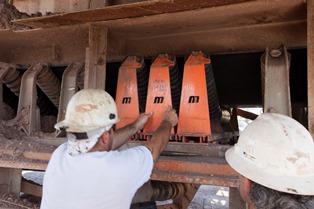
The efficient handling of coal on belt conveyors is essential to coal-fired power plants. The conveying of coal is prone to problems including the escape of spillage and airborne dust. These are typical problems, problems of long-standing, problems that continue to make the handling of coal a dirty, inefficient, unpleasant, high maintenance, low reward job.
A key to improving coal conveying is the implementation of advanced systems to improve performance and prevent fugitive material.
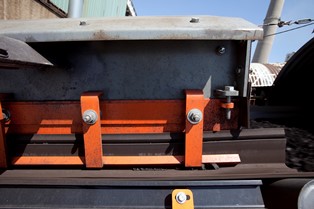
These advanced systems improve belt support and sealing systems, reduce maintenance requirements and allow maintenance work to be performed from safely outside enclosure and away from moving parts.
These advanced systems in coal conveying utilize the modern conveyor architecture. Safety and maintenance-friendly features are the dominant characteristics of this design standard. Some of the design innovations included in this new conveyor architecture include:
Slide-In/Out Components
To simplify maintenance in the new conveyor architecture, belt support systems such as impact cradles, support cradles and idlers incorporate track-mounted sub-assemblies that slide out on one side of the conveyor for maintenance. This service system will minimize conveyor downtime and enhance employee safety, as workers will no longer need to crawl into the structure to remove and replace components.
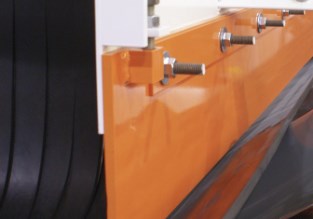
External Wear Liner
For years, wear liners have been installed on the inside of the transfer point’s skirt board, to help preserve the steel structure and protect the skirt board sealing system. But this internal liner proved too difficult to install and inspect, and even harder to replace. Now, the modern conveyor architecture has developed an external wear liner; that is, a liner that is mounted on the outside of the skirt board. External liners allow for safer installation and maintenance. The external wear liners effectively protect the skirt boards and the sealing system, yet are easily inspected and maintained or replaced without requiring confined space procedures.
Modular Chute Walls and Covered Skirtboard
Preventing the escape of fugitive material is another important aspect of modern conveyor architecture.
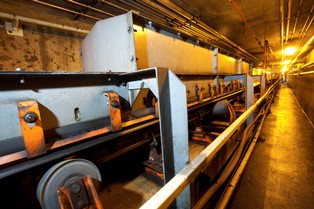
Pre-engineered modular chute wall, which simplifies the design and construction of transfer point skirt boards and stilling zones, will help to manage airflow and control dust. Skirtboard covers with a peaked roof form a settling zone to prevent escape of airborne dust from the conveyor loading zone, while improving safety by keeping workers away from moving cargo and rolling components.
These advanced conveyor technologies have already achieved improvements in operations and maintenance in coal-handling operations in terminals and power plants.
About The Author
Greg Bierie
Sales and Marketing Manager - Projects
As Sales and Marketing Manager - Projects, Greg is focused on the development and application of advanced conveyor technologies into bulk material handling industries. Greg has spent nearly 30 years serving mining, power generation and other industries with material handling systems, with responsibilities in project estimation, procurement, installation, project management and system design. He holds a B.S. from Colorado State University.